How to Manufacture Semiconductor Distributor in New York?
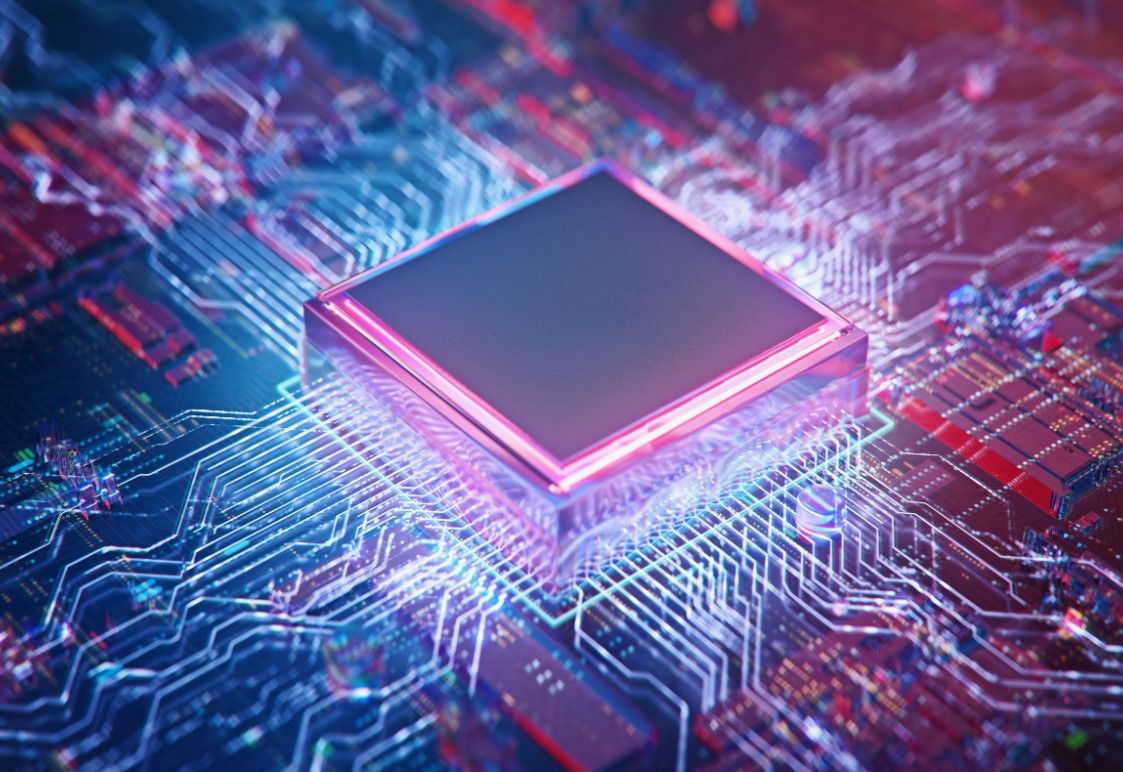
Manufacturing semiconductor distributors in New York involves a series of strategic steps and considerations. From establishing the necessary infrastructure to navigating regulatory requirements, this process demands careful planning and execution.
In this guide, we’ll delve into the essential aspects of manufacturing semiconductor distributors in New York, providing insights and actionable steps for success.
Market Research and Feasibility Analysis
Before diving into manufacturing semiconductor distributors, thorough market research and feasibility analysis are crucial. Identify the demand for semiconductor distributors in New York and evaluate the competitive landscape.
Analyze factors such as market size, growth trends, potential customers, and existing competitors. Additionally, assess the feasibility of manufacturing operations in New York, considering factors like infrastructure, workforce availability, and regulatory environment.
Establishing Legal and Regulatory Compliance
Compliance with legal and regulatory requirements is paramount in semiconductor manufacturing. Begin by registering your business entity and obtaining necessary permits and licenses to operate in New York.
Familiarize yourself with environmental regulations, safety standards, and intellectual property laws relevant to semiconductor manufacturing.
Establish robust quality control protocols to ensure compliance with industry standards and regulations.
Securing Financing and Investment
Manufacturing semiconductor distributors requires significant capital investment. Secure financing through a combination of equity, loans, and government incentives.
Explore financing options tailored to manufacturing businesses, such as grants, loans, and tax credits offered by state and federal agencies.
Develop a comprehensive business plan outlining financial projections, investment requirements, and potential returns to attract investors and lenders.
Building Infrastructure and Facilities
Invest in state-of-the-art infrastructure and facilities to support semiconductor manufacturing operations. Choose a strategic location in New York with access to transportation networks, utilities, and skilled labor.
Construct or retrofit facilities equipped with clean rooms, specialized equipment, and advanced manufacturing technologies.
Implement stringent security measures to protect intellectual property and sensitive information.
Procuring Equipment and Technology
Acquire cutting-edge equipment and technology essential for semiconductor manufacturing. Collaborate with reputable suppliers and manufacturers to source semiconductor fabrication equipment, materials, and components.
Invest in automation and robotics to streamline production processes and enhance efficiency. Ensure compatibility and scalability of equipment to accommodate future growth and technological advancements.
Semiconductor Distributor Recruiting and Training Talent
Recruit a skilled and diverse workforce capable of meeting the demands of semiconductor manufacturing. Partner with educational institutions and training providers to develop customized training programs for semiconductor technicians and engineers.
Emphasize continuous learning and professional development to keep pace with evolving technologies and industry best practices. Foster a culture of innovation, collaboration, and safety within the organization.
Implementing Quality Control and Assurance
Maintain rigorous quality control and assurance processes throughout the manufacturing process. Establish quality management systems to monitor and evaluate every stage of semiconductor production.
Conduct comprehensive testing and inspection to detect defects, ensure product reliability, and meet customer specifications.
Continuously improve processes and procedures based on feedback and data analysis to enhance product quality and customer satisfaction.
Establishing Supply Chain and Distribution Channels
Forge strategic partnerships with suppliers, distributors, and logistics providers to optimize the semiconductor supply chain. Ensure reliable and efficient procurement of raw materials, components, and equipment from domestic and international sources.
Develop robust distribution channels to deliver semiconductor distributor to customers in New York and beyond. Leverage technology and data analytics to optimize inventory management and logistics operations.
Implementing Sustainability Practices
Incorporate sustainability practices into semiconductor manufacturing to minimize environmental impact and enhance corporate social responsibility.
Adopt energy-efficient technologies, waste reduction strategies, and recycling initiatives to conserve resources and reduce carbon footprint.
Comply with environmental regulations and industry standards for hazardous materials handling and emissions control. Engage stakeholders and communities to promote transparency and accountability in sustainability efforts.
Continuous Improvement and Innovation
Embrace a culture of continuous improvement and innovation to stay competitive in the semiconductor industry. Invest in research and development to drive technological advancements and product innovation.
Encourage employee creativity and entrepreneurship to generate new ideas and solutions. Stay abreast of emerging trends, market developments, and disruptive technologies to anticipate and adapt to changes in the semiconductor landscape.
Conclusion
Manufacturing semiconductor distributors in New York is a complex yet rewarding endeavor. By following the strategic steps outlined in this guide and leveraging the resources and expertise available, you can establish a successful semiconductor manufacturing operation in New York. Stay agile, adaptable, and focused on delivering high-quality products to meet the evolving needs of customers in the semiconductor market.