Factors to Consider When Choosing a Phase Converter
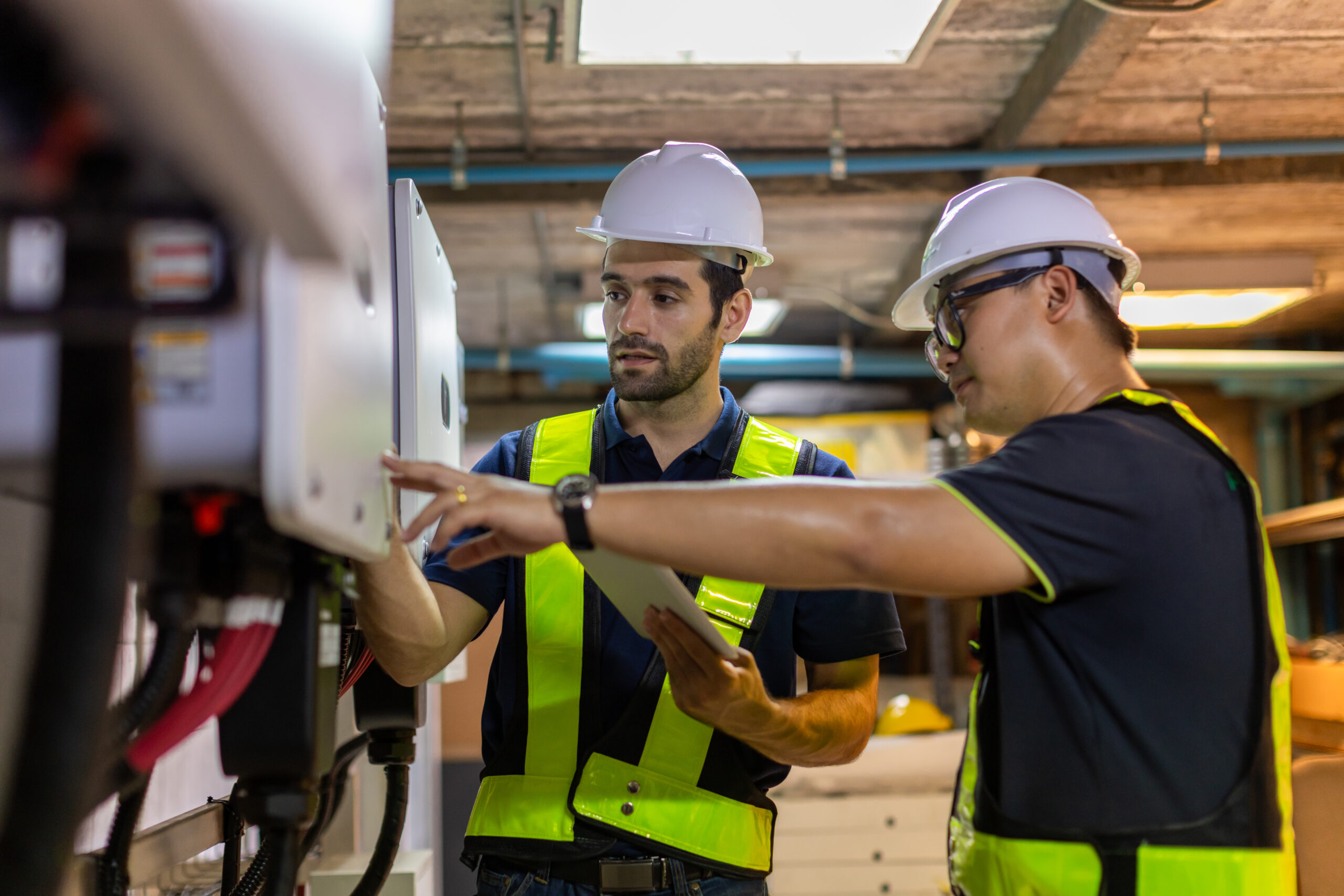
When setting up your industrial machinery or heavy-duty equipment, one crucial aspect often overlooked is the power supply. A three-phase power supply can be necessary for running certain types of machinery efficiently. However, not all facilities have access to three-phase power. This is where a phase converter becomes invaluable. Understanding the factors to consider when choosing a phase converter can save you time, money, and ensure your equipment operates smoothly.
Load Requirements
The first factor to look into is the load demand of your machinery. Understanding the overall horsepower (HP) or kilowatts (kW) needed by your equipment is vital in selecting the proper phase converter. Different types of machinery have variable power demands, and utilizing an inadequate converter might lead to inefficiency, operational troubles, or even damage to your equipment. For instance, heavy-duty industrial machinery often requires strong, high-load handling converters like rotary phase converters, which can manage considerable power demands with dependability and efficiency.
On the other hand, smaller or less demanding machines might function well with static phase converters, which are less costly but have limitations in terms of load capacity. Digital phase converters, while more expensive, offer precise power delivery and can adapt to a wide range of load requirements, making them suitable for versatile applications. Evaluating your machinery’s load requirements ensures you choose a converter that can handle the operational demands, providing stable and efficient performance.
Voltage and Amperage
Learning about the voltage and amperage needs of your equipment is vital when purchasing a phase converter. Each piece of machinery has distinct power needs, and selecting a converter that corresponds with these specs is vital for optimal operation. Ensure the phase converter can handle the input voltage available at your facility and give the necessary output voltage and amperage required by your equipment. For example, if your machinery demands 480V three-phase electricity but your converter can only give 240V, it wonāt perform appropriately, leading to inefficiency and potential operational concerns.
Additionally, an undersized converter could struggle to produce appropriate amperage, causing overheating, equipment malfunction, or even severe safety dangers like electrical fires. Conversely, over-specifying your converter might lead to unneeded costs. Therefore, matching the voltage and amperage precisely to your machinery’s requirements is crucial for assuring efficient operation, safety, and lifespan of both the converter and your equipment.
Efficiency and Power Quality
Efficiency is another key feature to consider when purchasing a phase converter. Generally, rotary and digital phase converters offer superior efficiency compared to static converters. This efficiency leads to better energy utilization, decreased operational expenses, and enhanced performance of your machinery. Power quality is another key part of efficiency, comprising issues like voltage balance, harmonic distortion, and overall power stability. Poor power quality can lead to irregular machinery behavior, increased wear and tear, and significant downtime.
Rotary converters are noted for their robust performance, maintaining acceptable power quality even under variable load situations. However, digital phase converters stand out for providing the highest power quality, with precise control over voltage and little harmonic distortion. For delicate or highly precise equipment, this leads to dependable and seamless functioning. Investing in a converter with high efficiency and outstanding power quality assures optimal machinery performance, longevity, and cost savings in the long run.
Cost and Budget
It is certain that your budget will play a role in the phase converter you select. Because they are the least expensive option, static phase converters are a good choice for smaller operations or less demanding applications. But they have drawbacks as well, such decreased load capacity and efficiency, which may limit their application to particular kinds of machinery. The cost and performance of rotary phase converters are balanced. They are appropriate for a variety of applications, especially those with higher load needs, due to their reasonable pricing and exceptional efficiency and dependable performance.
In contrast, digital phase converters are the priciest option, but their exceptional power quality, exceptional efficiency, and cutting-edge features make them worth the money. For tasks where accuracy and dependability are crucial, these converters are perfect. To make an informed decision that matches your budget and operational demands, it’s critical to balance the initial investment against long-term advantages and operating expenses, taking into account aspects like energy savings, maintenance requirements, and potential productivity increases.
Installation and Space Requirements
When selecting, take into account the area needed to install the phase converter. Compared to static or digital converters, rotary phase converters are larger and require more physical area for installation. They are renowned for their reliable performance and capacity to manage enormous loads. This size issue can be very important, particularly in establishments where room is limited. Furthermore, there are variations in the installation procedure for various kinds of converters. Rotary converters frequently require a more complicated setup, which can call for expert installation assistance.
This influences the amount of time needed to get the system up and running in addition to raising the overall cost. Due to their smaller size and ease of installation, static and digital converters have the potential to save money and installation time. Thus, choosing the appropriate phase converter for your facility and guaranteeing a seamless and effective setup process demand careful consideration of your available space and an awareness of the installation requirements.
Reliability and Maintenance
In industrial applications, where downtime can cause large losses, reliability is very important. Rotating phase converters are well known for their dependability, longevity, and low maintenance requirements. They are a dependable option for heavy-duty industrial settings because of their sturdy structure, which enables them to withstand large loads and variable demands. Static converters have the benefit of being relatively simple to maintain even though they are not as robust. Because of their more straightforward design, there are fewer parts that could go wrong, which translates to less maintenance work and expense.
Despite being more complicated, digital phase converters are incredibly reliable because of their sophisticated monitoring and troubleshooting capabilities. These capabilities ensure timely intervention and lower the risk of unplanned failures by enabling real-time tracking of performance metrics and early detection of possible faults. Purchasing a dependable phase converter is essential for industrial applications since it reduces maintenance costs and downtime while simultaneously increasing operational efficiency.
Key Takeaway
A number of aspects need to be carefully considered when selecting the best phase converter, including load requirements, voltage and amperage, efficiency, cost, installation, and reliability. You may choose a phase converter that guarantees your equipment operates effectively and efficiently and offers a dependable power source for your operations by carefully weighing these factors. Recall that purchasing the appropriate phase converter is an investment in the continuous and seamless operation of your equipment.