How CNC Retrofit Services Drive Efficiency in Precision Machining
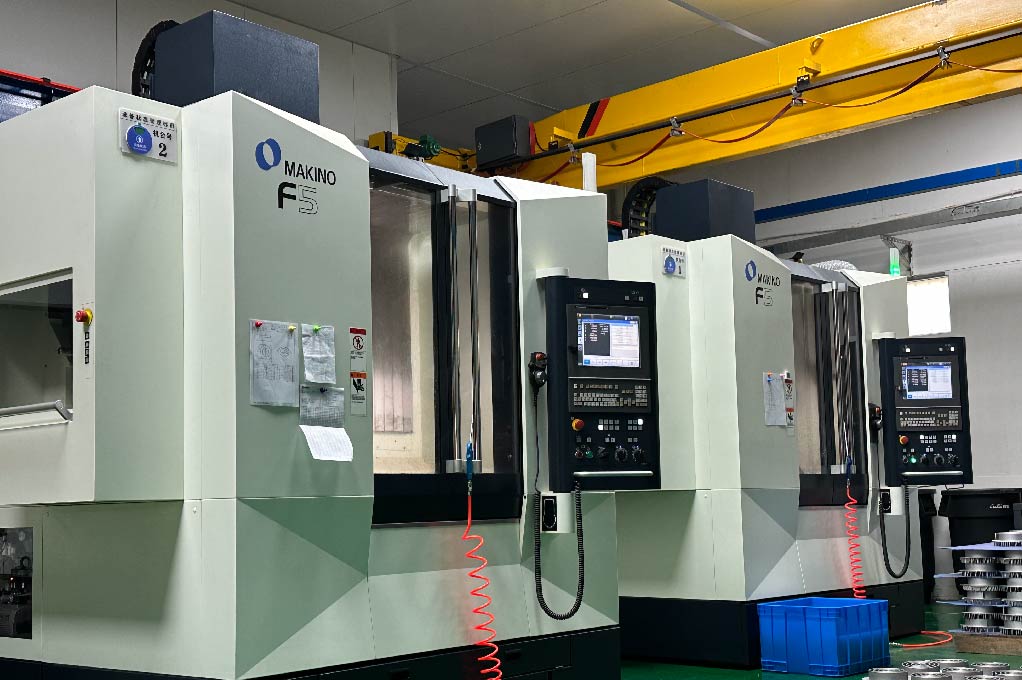
In the rapidly evolving world of precision machining, staying ahead of the curve is paramount. One key strategy that manufacturers are increasingly adopting to boost efficiency is the implementation of CNC retrofit services. In this comprehensive guide, we will explore how CNC retrofit services drive efficiency in precision machining and why businesses are turning to this innovative solution to upgrade their machining capabilities.
1. Understanding CNC Retrofit Services
CNC retrofit services involve the upgrading of existing machining equipment with state-of-the-art computer numerical control (CNC) technology. This process allows manufacturers to breathe new life into older machines, enhancing their performance, precision, and overall efficiency. By retrofitting existing equipment, businesses can avoid the significant costs associated with purchasing brand-new machinery while still reaping the benefits of advanced CNC capabilities.
2. Advantages of CNC Retrofit Services
A. Cost-Effectiveness:
One of the primary advantages of CNC retrofit services is the cost-effectiveness they offer. Purchasing new CNC machines can be a substantial investment, but retrofitting provides a more budget-friendly alternative. Manufacturers can upgrade their existing equipment, extending its lifespan and enhancing its capabilities without the hefty price tag associated with buying new machinery.
B. Improved Precision:
Precision is a critical factor in machining processes, and CNC retrofit services excel in this regard. Upgrading to CNC technology significantly enhances the precision of machining operations, leading to higher-quality end products. This increased precision is particularly beneficial for industries that demand intricate and accurate components.
C. Enhanced Efficiency:
Efficiency is a key driver for any manufacturing process. CNC retrofit services streamline operations by automating tasks, reducing human error, and optimizing production workflows. The result is a more efficient and productive machining environment that can handle higher workloads with greater ease.
D. Compatibility with Modern Software:
Retrofitting machines with CNC technology ensures compatibility with modern software applications. This compatibility opens up new possibilities for programming, monitoring, and adjusting machining processes, contributing to a more flexible and adaptable manufacturing system.
3. Case Studies
To illustrate the real-world impact of CNC retrofit services, we’ll delve into a couple of case studies. These examples will highlight specific instances where businesses successfully implemented retrofitting to achieve notable improvements in efficiency, precision, and overall machining capabilities.
4. Choosing the Right CNC Retrofit Service Provider
Selecting the right CNC retrofit service provider is crucial for a successful implementation. Factors to consider include the provider’s experience, reputation, and the range of services offered. By partnering with a reliable retrofitting specialist, manufacturers can ensure a seamless transition to upgraded CNC technology.
Conclusion
CNC retrofit services emerge as a strategic solution for manufacturers seeking to drive efficiency in precision machining. By leveraging the advantages of cost-effectiveness, improved precision, and enhanced efficiency, businesses can position themselves at the forefront of the industry. As technology continues to advance, embracing CNC retrofit services proves to be a forward-thinking approach to stay competitive in the ever-evolving landscape of precision machining.