Why Plastic Injection Molding Is the Future of Manufacturing
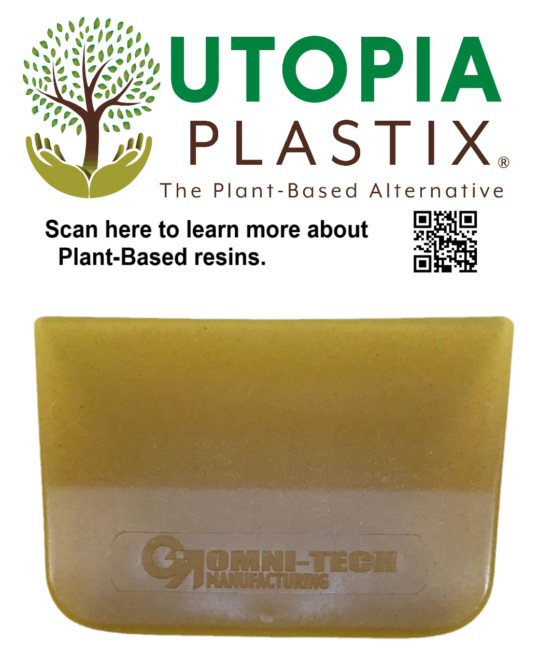
In odern manufacturing, few technologies have had as profound an impact as plastic injection molding. From intricate automotive components to everyday consumer goods, this innovative process has redefined how products are designed, produced, and distributed. Its versatility and efficiency make it not just a method of plastic manufacturing in Tennessee, but a cornerstone of industrial progress. Let’s delve into why plastic injection molding isn’t just a passing trend, but the definitive future of manufacturing in Tennessee and beyond.
Precision and Efficiency
Plastic injection molding offers unparalleled precision in manufacturing. It enables the production of complex shapes with consistent quality, making it ideal for industries demanding high accuracy. Manufacturers can achieve tolerances as tight as a few microns, ensuring that each part meets exact specifications without the need for extensive post-processing.
Cost-Effectiveness
By minimizing material waste and reducing labor costs, plastic injection molding proves cost-effective over traditional manufacturing methods. This efficiency makes it a preferred choice for both large-scale production and prototyping. Companies can achieve economies of scale due to high production output and streamlined processes, leading to lower per-unit costs and improved profitability.
Versatility Across Industries
From automotive to medical devices and consumer electronics, plastic injection molding caters to diverse industry needs. Its ability to handle various materials such as thermoplastics, elastomers, and polymers ensures versatility in manufacturing applications. Whether producing small, intricate parts or large, structural components, injection molding provides flexibility to meet a wide range of product requirements.
Rapid Prototyping
Speed is crucial in product development. Plastic injection molding allows for rapid prototyping, enabling companies to iterate designs quickly and bring products to market faster than ever before. This rapid turnaround time reduces time-to-market, giving businesses a competitive edge in responding to consumer demands and market trends swiftly.
Durability and Strength
Modern polymers used in injection molding offer enhanced durability and strength characteristics. This durability ensures products can withstand rigorous use and environmental conditions, meeting stringent performance standards across industries. Whether creating components for automotive applications or electronics, injection-molded parts maintain integrity and reliability under various stressors and environmental factors.
Environmental Sustainability
With growing concerns over environmental impact, plastic injection molding has evolved to minimize waste through efficient material usage and recycling practices. Manufacturers can optimize material distribution within molds to reduce scrap and enhance resource efficiency. Additionally, advances in biodegradable and recyclable materials further support sustainable manufacturing practices, aligning with global efforts towards environmental stewardship.
Innovation in Design
The design freedom provided by injection molding allows engineers to create intricate geometries and innovative features that enhance product functionality and aesthetics. Complex part geometries, such as undercuts and overhangs, can be achieved with multi-cavity molds and advanced tooling techniques. This design flexibility encourages creativity in product development, enabling companies to differentiate their offerings and meet evolving consumer preferences.
Local Manufacturing Advantages
Tennessee’s strategic location and robust manufacturing ecosystem make it an ideal hub for plastic injection molding. Proximity to major markets and skilled labor contribute to its appeal for manufacturers seeking operational efficiency and logistical advantages. Local production facilities benefit from reduced shipping costs and lead times, supporting just-in-time manufacturing strategies and enhancing supply chain resilience.
High Production Consistency
Injection molding ensures consistent part quality and reproducibility batch after batch. This reliability is crucial in industries requiring standardized components with minimal variation, such as medical devices and automotive parts. Manufacturers can rely on injection molding to maintain strict quality control measures and meet regulatory standards consistently.
Enhanced Design Flexibility
Advanced technologies in plastic injection molding, such as overmolding and insert molding, offer enhanced design flexibility. These techniques allow for the integration of multiple materials and components within a single part, optimizing functionality and reducing assembly costs. Such versatility is advantageous in creating innovative products that meet evolving market demands.
The Bottom Line
In Tennessee, plastic injection molding is not just a manufacturing process; it’s a catalyst for innovation and efficiency across industries. Its ability to combine precision, versatility, and sustainability makes it indispensable in the modern manufacturing landscape, particularly in Tennessee. As technology advances and demands evolve, plastic injection molding will continue to shape the future of how we make products, driving progress and meeting the diverse needs of consumers worldwide.
Whether producing intricate medical devices or durable automotive components, the benefits of plastic injection molding are clear. It’s more than a manufacturing method; it’s a gateway to innovation and efficiency, shaping the future of industry in Tennessee and beyond.