Why are Injection Molded Parts Ideal for Medical and Food Applications?
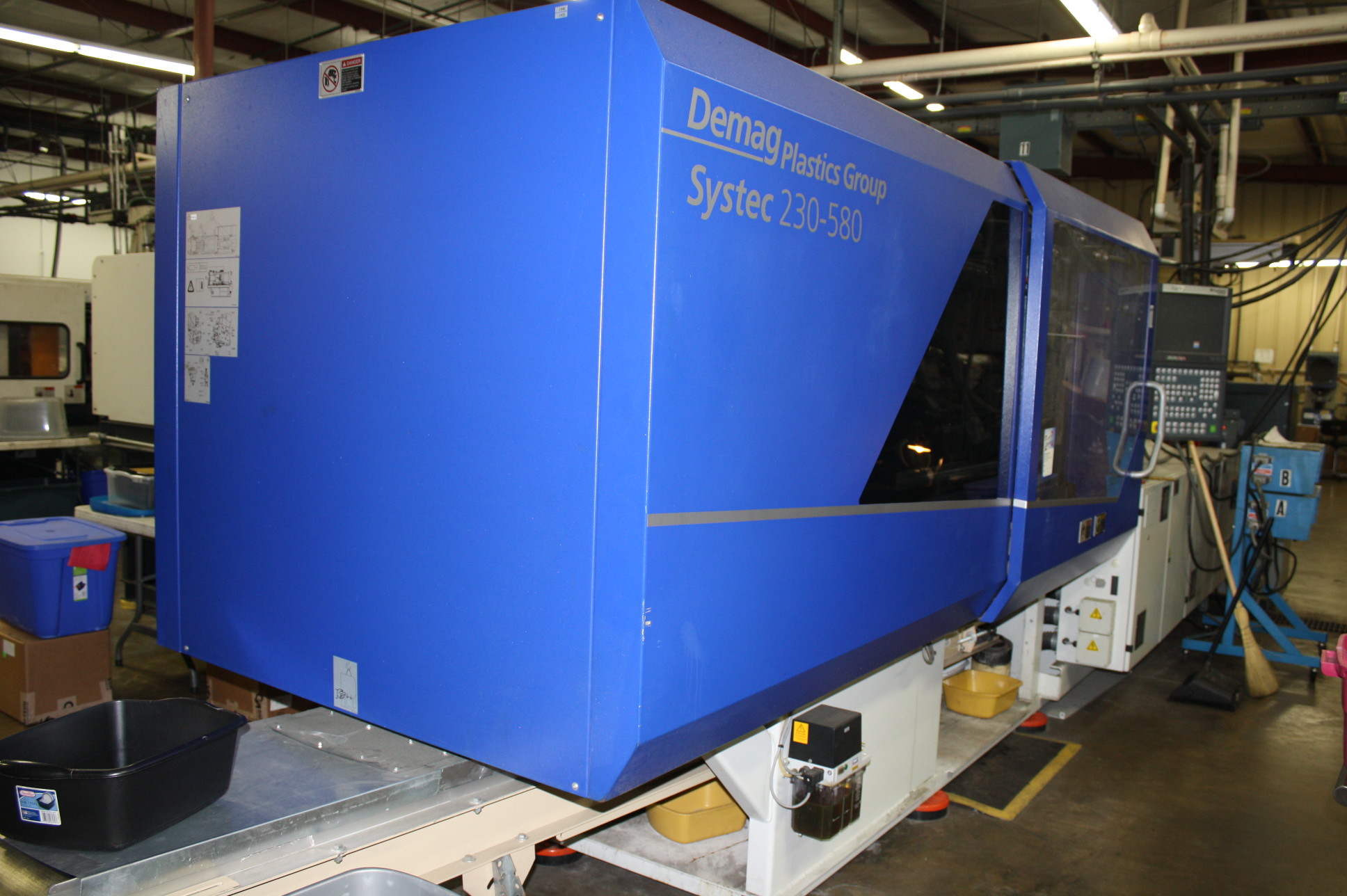
Plastic part manufacturing, specifically through injection molding, has catalyzed significant advancements in industries where precision, cleanliness, and reliability are non-negotiable—most notably, within the realms of medical and food applications. The process of injection molding enables the production of plastic parts with unparalleled accuracy and consistency, making it a preferred choice for critical environments where quality and performance are paramount.
Why are Injection Molded Parts Ideal for Medical and Food Applications?
Injection molding stands out in the medical and food sectors due to its ability to meet stringent regulatory requirements while offering exceptional performance characteristics.
Sterilizability and Cleanliness
 Medical and food-grade plastics used in injection molding are engineered to withstand rigorous sterilization processes, ensuring that components maintain their integrity and cleanliness throughout their lifecycle. From surgical instruments to food containers, these materials uphold the highest standards of hygiene.- Precision and Consistency The injection molding process excels in Plastic part manufacturing with tight tolerances and intricate designs, ensuring uniformity across large production runs. This level of precision is crucial in medical devices where accuracy directly impacts patient outcomes and in food packaging where consistency ensures product safety.
- Material Selection and Compliance  Manufacturers can select from a wide range of FDA-approved and biocompatible materials suitable for medical and food applications. This versatility allows for tailored solutions that meet specific regulatory and performance requirements, ensuring compliance with industry standards.
- Cost-Effectiveness  Despite initial setup costs, injection molding proves cost-effective for high-volume production due to its rapid cycle times and minimal material wastage. This efficiency is particularly advantageous for producing disposable medical consumables and mass-produced food packaging, optimizing operational expenses over time.
- Complex Geometries and Functional Design  Injection molding enables the creation of intricate part geometries with features such as undercuts, thin walls, and complex surface textures. This capability is essential for designing ergonomic medical devices that enhance user comfort and functional food packaging that improves shelf life and convenience.
- Durability and Performance
 Plastic parts manufactured through injection molding exhibit excellent durability, impact resistance, and dimensional stability. These properties ensure the reliability and longevity of medical instruments under demanding conditions and the robustness of food containers throughout handling, storage, and transportations.
Final Remarks
Injection molding plastic parts are indispensable in the medical and food industries due to their sterilizability, precision manufacturing capabilities, material versatility, cost-effectiveness for large-scale production, ability to produce complex designs, and reliable performance attributes. As these sectors continue to evolve with technological advancements, injection molding remains at the forefront, driving innovation and setting benchmarks for safety, quality, and efficiency in healthcare and food service industries globally.