The Power of Aluminum Extrusion
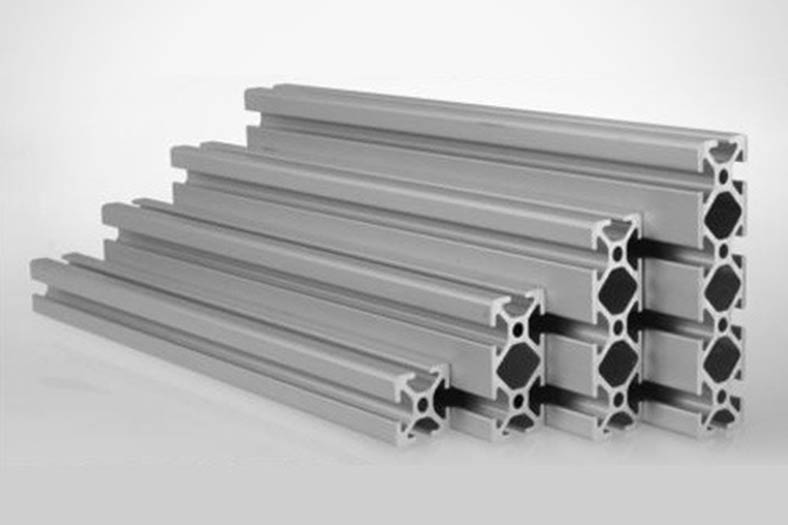
India’s strategic geographical place, considerable natural resources, and skilled workers have made it a good vacation spot for aluminum extrusion organizations. These agencies boast cutting-edge production centers ready with advanced extrusion presses and modern technology. This permits them to produce terrific aluminum extrusions that meet stringent global requirements. Aluminum extrusion companies in India have emerged as key game enthusiasts in the international aluminum industry, contributing considerably to the United States’ financial growth. These businesses recognize the need to transform aluminum billets into a huge variety of extruded profiles through a unique method of heating, shaping, and cooling. This versatile manufacturing method allows for the creation complex shapes and complicated designs, catering to various industries inclusive of construction, cars, aerospace, electronics, and more. By embracing innovation and sustainable practices, aluminum extrusion organizations in India are poised to preserve their increased trajectory and solidify their role as worldwide leaders in the aluminum enterprise.Â
Benefits of Aluminum Extrusion
- Versatility:
The versatility of aluminum extrusions is likewise glaring in the extensive style of finishes and coatings to be had. Anodizing, powder coating, and portraying can be applied to aluminum extrusions to enhance their look, sturdiness, and corrosion resistance. These finishes no longer best offer aesthetic appeal but moreover protect the underlying metal from environmental factors, extending its lifespan.
This versatility stems from the ability to tailor the alloy composition and extrusion manner to obtain precise homes, consisting of power, corrosion resistance, and thermal conductivity. By carefully selecting the proper alloy and adjusting the extrusion parameters, producers can create extrusions with a huge variety of mechanical and bodily homes. For instance, high-electricity alloys may be used for structural programs, at the same time as warmth-treatable alloys may be hired for additives that require greater electricity and durability.
- Strength and durability:
Aluminum extrusions are famed for their splendid electricity and durability, making them best for an extensive range of packages. This aggregate of residences is completed through cautious alloy selection, unique extrusion procedures, and powerful put-up-processing treatments. Aluminum alloys, inclusive of those containing magnesium, copper, and zinc, showcase high electricity-to-weight ratios, allowing the advent of lightweight yet sturdy structures. This is especially beneficial in industries that encompass aerospace and vehicles, wherein weight loss is essential for gasoline performance and average performance. Heat treatment techniques, consisting of solutions and growing older, answers beautify the mechanical homes of aluminum extrusions, resulting in improved hardness, electricity, and fatigue resistance. Additionally, aluminum’s herbal corrosion resistance, coupled with defensive coatings like anodizing and powder coating, ensures prolonged-lasting durability even in harsh environments. This inherent corrosion resistance, mixed with shielding coatings, safeguards aluminum extrusions from degradation, extending their lifespan and making them suitable for outdoor programs.
- Cost-effective:
Aluminum extrusion offers a cost-powerful solution for manufacturing complicated shapes and profiles. By eliminating the need for enormous machining and welding, this method notably reduces labor and fabric fees. Additionally, the excessive production rates conceivable via extrusion limit production time, leading to decreased basic production expenses. Furthermore, the excessive power-to-weight ratio of aluminum extrusions permits the usage of thinner sections, lowering the amount of cloth required. This, combined with the recyclability of aluminum, further contributes to the value-effectiveness of this production system.
For instance, consider the production of a vehicle frame. Traditionally, automobile frames were made from metallic, which required vast welding and machining. However, with aluminum extrusion, the frame can be produced in a single piece, doing away with the need for welding and notably lowering the amount of machining required. This consequences in a lighter, more potent, and greater value-effective frame.
- Machinability:Â
Aluminum extrusions are renowned for their exquisite machinability, making them a versatile preference for a huge range of applications. This asset stems from the steel’s softness and low slicing forces, making an allowance for green machining operations. Various machining strategies, which include drilling, milling, turning, and tapping, can be easily achieved on aluminum extrusions to create complex shapes and specific capabilities. The low warmness generation at some point of machining minimizes thermal stresses, decreasing the threat of distortion and enhancing dimensional accuracy. Additionally, the availability of specialized cutting gear and lubricants further complements the machinability of aluminum, permitting manufacturers to achieve top-notch finished products.
- Recyclability:
Aluminum is one of the maximum recycled materials on Earth, and its recyclability is a vast aspect of its sustainability and great use. This inherent asset makes it an environmentally pleasant desire for diverse packages. The recycling approach of aluminum is pretty smooth and green. Used aluminum merchandise, which incorporates beverage cans, car additives, and advent materials, is amassed and taken care of. These materials are then transported to recycling centers where they may be shredded and melted. The molten aluminum is delicate to put off impurities and cast into ingots. These ingots may be similarly processed into new aluminum products, which include extrusions, without any lack of niceness. Â Â
One of the key advantages of aluminum recycling is its energy performance. Recycling aluminum requires considerably less strength than producing number one aluminum from bauxite ore. Recycling aluminum can store as much as 95% of the electricity required for primary production. This strength saving is related to decreased greenhouse gasoline emissions and a smaller carbon footprint. Furthermore, aluminum is infinitely recyclable, meaning it can be recycled time and again with no degradation in its houses.
Aluminum extrusion is a flexible production manner that involves shaping aluminum alloy into diverse go-sectional profiles. This system is executed by heating aluminum billets to a malleable nation and forcing them through an exactly engineered die. The die imparts the preferred form to the extruded aluminum, which is then cooled and solidified. One of the most putting examples of the versatility and aesthetics of aluminum extrusions is black anodized aluminum. This stop offers a graceful, present-day observe the equal time as enhancing the sturdiness and corrosion resistance of the material. Black anodized aluminum is widely used in architectural applications, automotive design, and consumer electronics, showcasing the enduring appeal and functional excellence of aluminum extrusions.