Precision Gear VS Standard Gearing: The Ultimate Showdown
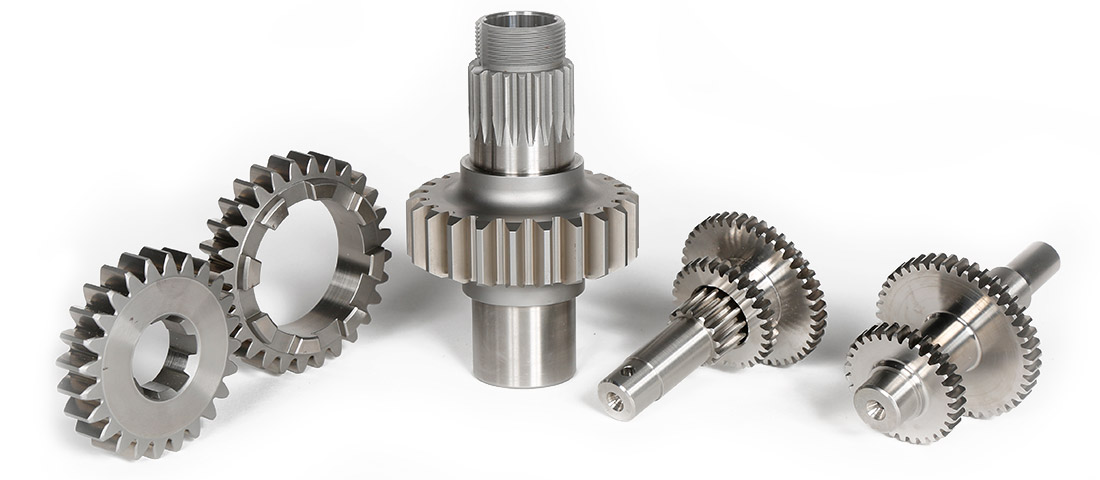
In the realm of machinery, Precision Gear and Standard Gearing engage in the ultimate showdown. This article delves into the intricacies of both, highlighting their strengths and weaknesses to determine which reigns supreme in the world of mechanical precision. Elevate your machinery with precision and reliability. As a leading Precision Gear Manufacturer, we craft gears with meticulous accuracy, ensuring optimal performance. Trust us for cutting-edge solutions that drive your machinery to new heights of efficiency.
Precision Gear: Unraveling the Intricacies
Here’s why Precision Gear stands out. Precision gears are crafted with meticulous attention to detail, ensuring tight tolerances and minimal backlash. The manufacturing process involves cutting-edge technology, resulting in gears that deliver unmatched accuracy and performance, making them ideal for applications demanding the highest levels of precision.
Standard Gearing: The Familiar Approach
Standard gearing, while reliable, operates on a broader scale. The manufacturing process allows for faster production and lower costs, making it suitable for applications where precision is not the top priority. However, the trade-off often lies in tolerances and accuracy, which may not meet the stringent requirements of precision-centric applications.
Strength and Efficiency
Precision gears excel in transmitting power efficiently. The tight tolerances reduce friction and wear, ensuring optimal energy transfer. Standard gearing, while efficient, may experience more power loss due to tolerances and backlash. The battle for strength and efficiency unfolds as each type contends for supremacy.
Applications in Focus
Here’s why Precision Gears dominate in specific applications. Industries such as aerospace, robotics, and medical devices demand the precision that only Precision Gears can deliver. Meanwhile, Standard Gearing finds its niche in applications where cost-effectiveness and reliability outweigh the need for pinpoint accuracy.
The Quest for Durability
Precision gears, with their superior manufacturing process, often exhibit enhanced durability. The precise tooth profiles and high-quality materials contribute to longer gear life. Standard gearing, while durable, may require more frequent maintenance and replacements, especially in high-stress environments. The showdown intensifies in the quest for long-lasting durability.
Cost Considerations
Precision comes at a cost. Precision gears, with their meticulous manufacturing process, tend to be pricier. Standard gearing, on the other hand, offers a more budget-friendly option. The choice between the two hinges on the specific needs of the application, balancing precision requirements with budget constraints.
Innovation and Advancements
Here’s why Precision Gears lead in innovation. Continuous advancements in materials and manufacturing technologies push the boundaries of what precision gears can achieve. Standard gearing, while reliable, may lag in adopting the latest innovations, affecting its competitiveness in cutting-edge applications.
Conclusion: The Verdict
In the ultimate showdown between Precision Gear and Standard Gearing, the victor emerges contextually. Precision gears showcase unparalleled accuracy and efficiency, making them the clear choice for applications demanding top-tier precision. Standard gearing, while cost-effective and reliable, finds its strength in less precision-sensitive environments. The ultimate decision rests on the unique requirements of the machinery in question, as the battle between precision and practicality continues to shape the mechanical landscape.