Modern Manufacturing Execution Systems (MES) and Operations Management
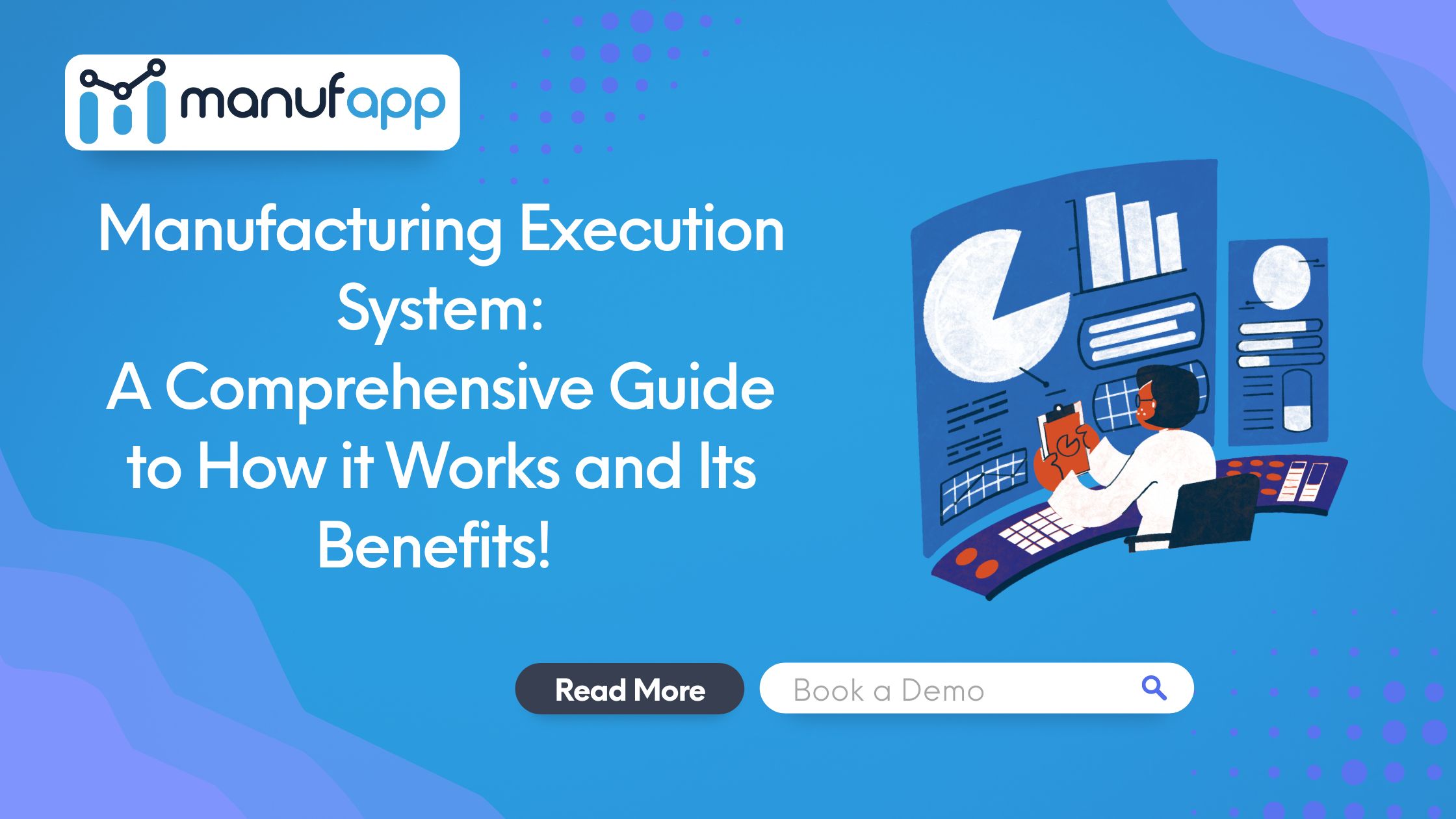
Manufacturers are always looking for methods to increase productivity, cut expenses, and streamline their operations in the fast-paced industrial world of today. Utilizing cutting-edge technology like Manufacturing Execution Systems (MES) and Manufacturing Information Systems (MIS) is essential to reaching these objectives. These systems are revolutionizing manufacturing operations and helping companies better control their production processes. The vital role that Manufacturing Operations Management (MOM), MES, and MIS play in transforming contemporary manufacturing will be examined in this blog.
Knowing how Manufacturing Execution Systems (MES) operate
An all-inclusive software program that offers real-time manufacturing process monitoring and control is called a Manufacturing Execution System (MES). MES ensures smooth data flow and communication across various manufacturing process levels by bridging the gap between shop floor operations and enterprise resource planning (ERP) systems.
An MES’s main job is to monitor and manage the production process from the receipt of raw materials to the delivery of the final product. It assists manufacturers in tracking equipment performance, managing work orders, keeping an eye on inventory, and guaranteeing product quality. Manufacturers can make data-driven choices, streamline processes, and resolve problems as they emerge with the help of MES, which gives them real-time visibility into production activity.
The following are some main advantages of MES implementation
Real-Time Data Access: MES enables producers to make prompt decisions by giving them access to real-time data regarding inventory levels, equipment performance, and production status.
Enhanced Efficiency: MES assists firms in streamlining their processes and cutting downtime by automating production scheduling and minimising manual intervention.
Enhanced Quality Control: By keeping an eye on production procedures and spotting possible problems before they affect the finished product, MES makes sure that quality standards are fulfilled.
Cost Reduction: MES helps cut waste, enhance resource use, and lower production costs by providing greater insight into production activities.
Manufacturing Information Systems’ (MIS) Function
The collection, storing, and analysis of data pertaining to manufacturing processes are all included in the more general term known as a Manufacturing Information System (MIS). By combining data from multiple sources, including as ERP systems, supply chain management tools, and financial systems, MIS offers a more thorough understanding of the manufacturing process than MES, which is primarily concerned with real-time production control.
Manufacturers can gain insights into key performance indicators (KPIs) including production rates, cycle times, and defect rates by using MIS to collect and analyse data from various stages of production. Making well-informed judgements regarding resource allocation, process enhancements, and overall performance optimisation need this knowledge.
Among the benefits of a successful MIS are:
Data-Driven Decision Making: By gathering and analysing vast amounts of data, MIS helps firms make well-informed choices on resource management and production procedures.
Performance Monitoring: By offering a comprehensive perspective of production performance, MIS assists manufacturers in locating inefficiencies, bottlenecks, and potential improvement areas.
Strategic Planning: MIS facilitates long-term strategic planning by combining data from several sources, allowing manufacturers to match their operations with market demands and corporate objectives.
The term “manufacturing operations management” (MOM) describes the collection of procedures and tools used to oversee and improve manufacturing operations. Production planning, scheduling, quality control, inventory management, and maintenance are just a few of the many tasks that fall under the umbrella of MOM. It offers a cohesive method of managing the complete production lifecycle by integrating systems such as MES and MIS.
Making sure that manufacturing processes are efficient, effective, and compliant with quality standards is the aim of MOM. MOM solutions give manufacturers the resources they need to improve customer satisfaction, lower downtime, optimise production schedules, and improve product quality.
Among the essential elements of Manufacturing Operations Management are:
Production Scheduling and Planning: Using production capacity, resource availability, and demand projections, MOM assists firms in planning and scheduling production runs. This guarantees that production is in line with market demands and client orders.
Quality Management: MOM has resources for keeping an eye on and managing product quality throughout the whole manufacturing process. Manufacturers can decrease faults and raise customer satisfaction by spotting and fixing quality problems early in the process.
Maintenance Management: To reduce downtime and guarantee that machines are running as efficiently as possible, MOM assists manufacturers in scheduling preventative maintenance and monitoring the operation of their equipment.
Supply Chain Integration: By integrating with supply chain management systems, MOM solutions guarantee the timely availability of components and raw materials, minimising stockouts and delays.
The Cooperation Among MIS, MOM, and MES
Although MES, MIS, and MOM each have unique functions in manufacturing processes, their combined use and integration yields the best results. MOM guarantees overall operational efficiency, MIS provides data analysis and insights, and MES allows real-time control of manufacturing processes. Manufacturers can attain a comprehensive approach to production management that promotes operational excellence and continuous development by integrating these systems.
For instance, MIS analyses real-time production performance data from MES to find patterns and areas that need improvement. . Manufacturers are able to make data-driven decisions and constantly improve their operations thanks to this integration’s feedback loop.
Conclusion
The manufacturing sector is undergoing a change thanks to the integration of Manufacturing Execution Systems (MES), Manufacturing Information Systems (MIS), and Manufacturing Operations Management (MOM). These technologies enable firms to analyse performance data, optimise operations for increased efficiency and cost savings, and monitor and control their manufacturing processes in real time.
MES, MIS, and MOM give manufacturers the tools they need to remain competitive in a market that is always changing as they face mounting pressure to satisfy consumer demands, cut expenses, and enhance product quality. Manufacturers can boost their overall business performance, stimulate innovation, and increase operational efficiency by using these solutions.
The secret to maximising the potential of contemporary manufacturing operations is integrating MES, MIS, and MOM into a unified manufacturing strategy. Data-driven manufacturing is the way of the future, and companies that embrace these technologies will be well-positioned to prosper in a market that is becoming more competitive and complex.
This article offers a thorough summary of the ways in which Manufacturing Operations Management (MOM), Manufacturing Execution Systems (MES), and Manufacturing Information Systems (MIS) are revolutionising the manufacturing sector. Manufacturers can improve decision-making, streamline processes, and promote continuous improvement by concentrating on the integration of various systems.